The Hysopt white paper “The High Cost of HVAC under-performance” laid out the case that:
- Performance Gaps in buildings are a pervasive issue, causing buildings to consume up to twice the amount of energy expected at the design stage;
- Under-performance of HVAC systems are a significant contributor to performance gaps;
- The growing requirement to decarbonise the way buildings are heated and ongoing energy price inflation compared to pre-pandemic levels exacerbate the issue further still;
In this article, we delve deeper into the three fundamental root causes that the white paper identifies as perpetuating HVAC system performance gaps:
- Outdated engineering tools – that are no-longer sophisticated or advanced enough to cope with increasing HVAC system design and engineering complexity;
- Communication gaps – including the fundamental disconnections that occur between the different parties in the supply chain;
- Ineffective As-Built Information – leading to sub-optimal management of the system and long-term operational under-performance;
For professionals in energy or buildings and estates management, understanding and addressing these issues is crucial for achieving optimal HVAC system performance.
1. Coping with increased HVAC system complexity:
Modern HVAC systems are becoming increasingly complex, with generation technologies such as heat pumps and hybrid installations becoming increasingly sensitive to operating conditions (such as temperatures and flow rates) to perform at their maximum expected efficiency. Marrying new technologies into legacy installations also poses problems.
In a recent survey conducted by Hysopt, 86% of energy and estates professionals from the healthcare and higher education sector revealed that they typically rely on the expertise of their supply chain to provide advice and technical assurance related to design and renovation of their HVAC installations.
Over simplification
However, the engineering tools in use today by these “trusted advisors” often over-simplify complex engineering issues by accounting only for operation of the HVAC system in peak load conditions, neglecting the dynamics of partial load operation, where the system operates most of the time. In fact, many engineering companies tell us that they are largely reliant on incredibly complex Excel spreadsheets to make their calculations – but with so many variables and “moving parts” these days, this approach is no longer adequate.
Modeling uncertainty
Furthermore, energy modeling software, primarily used for compliance in early design stages, oversimplifies HVAC system design as purely a thermal problem, disregarding essential hydraulic and control aspects. For example, in the real world systems do not respond “instantly” to changes in demand. This leads to inaccurate predictions and an inability to objectively compare the likely real world behavior and performance of different system concepts. Modeling uncertainty due over-simplification is a factor already referenced in CIBSE’s TM61 Operational Performance of Buildings as a contributing root cause of energy performance gaps.
Take for example a hybrid installation of a gas boiler, gas CHP and a heat pump. Energy modeling predictions might assume the annual energy contribution of each to “optimal” – biased towards lowest energy cost or carbon impact as required. However the truth of what will really happen in real life is largely left to assumptions and the reality is often somewhat different to expectations
The devil is in the detail
Moving beyond concept design, correctly specifying system components (for example pumps and control valves) becomes crucial. While specialist tools from manufacturers aid component selection, these focus on individual, specific component types, neglecting the interconnected nature of systems as a whole, where the selection of all hydraulic components is interdependent on each other. This approach, often spreadsheet-based and centered on peak load requirements, hinders understanding the holistic system behavior. In other words the designer is “blind to the whole system view”.
Over sizing
Furthermore, this lack of knowledge about whole system performance during the design stage prompts the addition of unnecessary margins to cover the risk of unknowns, leading to systems that are subsequently oversized. Research by Hysopt reveals that traditional static-load and rule-of-thumb approaches result in significant oversizing (50-95%, sometimes over 200%), escalating capital and energy costs while compromising occupant comfort.
Ultimately, calculation limitations of software tools being used result in a combination of oversimplification, assumptions, and over-sizing, in turn contributing to poor design choices being made and systems that already have “baked-in” performance gaps, before they are even constructed.
2. Bridging Disconnections in the Supply Chain
Secondly, problems occur due to lack of transparency and poor communication between the myriad of different stakeholders in the value chain.
Throughout the design/build/commission/operate process, communication gaps arise due to siloed working, misaligned priorities and a lack of consistent data flow between multidisciplinary teams at one stage of a project and the next.
Requirements to accept designs and specifications provided by others with no transparency of assumptions made leads to the addition of margins for error on top of margins for error in order to mitigate risk. Meanwhile inconsistency between the specific design and calculation tools being used at each stage by each stakeholder also prevents consistency, transparency and seamless collaboration.
Aligning priorities
Misaligned priorities among different stakeholders in the HVAC system life cycle can also become a problem. Inevitably, emphasis on delivering projects within squeezed capital cost budgets comes at the (often hidden) consequence of increases in operational energy cost of environmental performance, simply because the operational impacts of engineering choices made for the purposes of “value engineering” cannot be accurately quantified and are subject, at best, to estimates and optimism bias.
In our survey 57% of respondents told us that they felt their supply chain was ineffective at communicating the impacts of design decisions taken on operational performance KPI’s.
Internal communication gaps, especially between operational teams focused on operational metrics such as energy costs and (increasingly) environmental factors, and capital projects teams focused primarily on CAPEX budgets and delivery timescales, create additional challenges. Aligning priorities and fostering effective communication between these parties is essential. Many tell us “whole life costs” are an important metric in their projects (balancing operational vs investment costs) but when pressed, admit that quantifying the operational cost impact of a proposed CAPEX saving is often impossible to predict with any certainty.
Furthermore, we commonly here that risks of operational underperformance are backed off against design and build contracts. While this neatly shifts to burden of responsibility and the design and installation stages, operational estates teams still end up with systems that do not perform as originally expected and subsequently need to deal with the consequences. Soft landings schemes go some way to mitigating this issue, but without the correct tools in the first place to understand the “whole system view”, contractors and consultants are unable to easily pinpoint the root causes of the underperformance.
3. Ineffective As-Built Information – Beyond the Blueprint:
The segmented disciplines of architects, building services engineers, contractors and their sub-contractors are often all involved in various stages of a building’s development process but leave once the building is physically complete. The end-users then occupy a building that may be underperforming for reasons that they are unlikely to fully understand.
Traditionally, the information about the HVAC installation provided at hand over tends to focus on details of the physical assets (including data sheets, P&ID’s, DesOps and commissioning reports, etc), but typically these are in paper (or some other static digital form). Even a BIM model is only static. While these files give an indication of what the “as-built” installation looks like, it doesn’t provide any detail about how the system should or will perform.
For example – it should be possible to tell how the installation was commissioned – but this does not tell us whether the installation was commissioned correctly or for optimal performance in the first place!
Systems are also upgraded and expanded over time – especially in large, complex installations. But yet nobody has any clear idea of what impacts making additions, or adding extra capacity to the installation will have on the performance of what is already there.
Finally, information is fed through to the CAFM (computer aided facility management) systems from the BIM model, but this contains no information about how the installation should be correctly commissioned or even whether the components selected are correctly specified – because there is no link to a system level calculation model. Components are replaced over time as part of preventative or responsive maintenance, but once again, without any consideration or knowledge of what impact this will have on overall system performance.
Whole system performance
In fact, even if an optimally performing HVAC system is handed over, over time the performance of the system starts to drift because of some components start failing – pumps blocking, valves break, etc – or user maintenance intervention adjusts valve settings, BMS settings and so on..
Typically these may be interventions to try and correct comfort complaints. However, the cause of the problem is very difficult to identify because there is insufficient documentation nor a clear understanding of how the system really works. This leads to a lot of trial and error to solve problems which often only makes the problems worse ad only the symptoms are being addressed rather than the root causes.
Conclusion
Addressing the root causes of performance gaps in HVAC systems is crucial for professionals in energy or buildings and estates management. Ensuring their “expert” supply chain is using adequate and up to date engineering tools; fostering effective communication between multi-disciplinary teams; and enhancing the quality of as-built information used to operate and maintain systems over the long term are all pivotal steps toward achieving optimal HVAC system performance.
HVAC system Digital Twins of course provide such a solution.
They address the first problem by providing Innovative Engineering Tools able to provide advanced computational analysis to allow all participants in the project to optimise and adapt the system design at every stage. Using physics-based analysis, detailed insights of how even the most complex of system configurations will perform can be simulated and optimised before its even constructed.
This way, engineering and performance is shifted from a “component-level” approach to a “system-level” approach.
Seamless communication is enabled between all parties in the engineering chain, promoting collaboration, breaking down silos and enabling real-time data sharing.
Teams can work concurrently on a single model, reducing conflicts, improving project efficiency and minimising the risk of performance gaps emerging.
And finally, the digital twin of the final as-built installation becomes a Digital Asset for complete lifecycle management of the installation throughout the operational phase, representing not just the physical installation, but also its performance, maintenance, and operation.
This supports more effective facility management and asset operations and ensures the installation can continue to perform optimally throughout its operational life.
Explore more
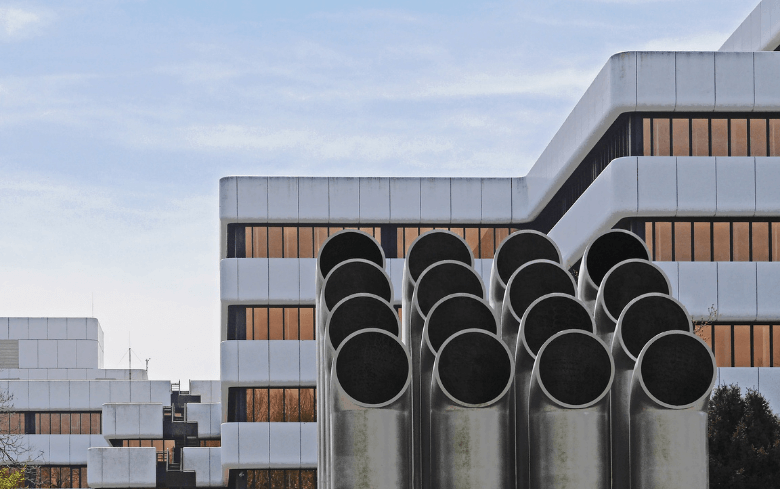
Step inside the inner-workings of your HVAC-installation
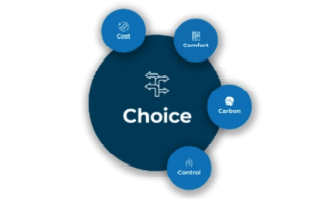
The choice is yours
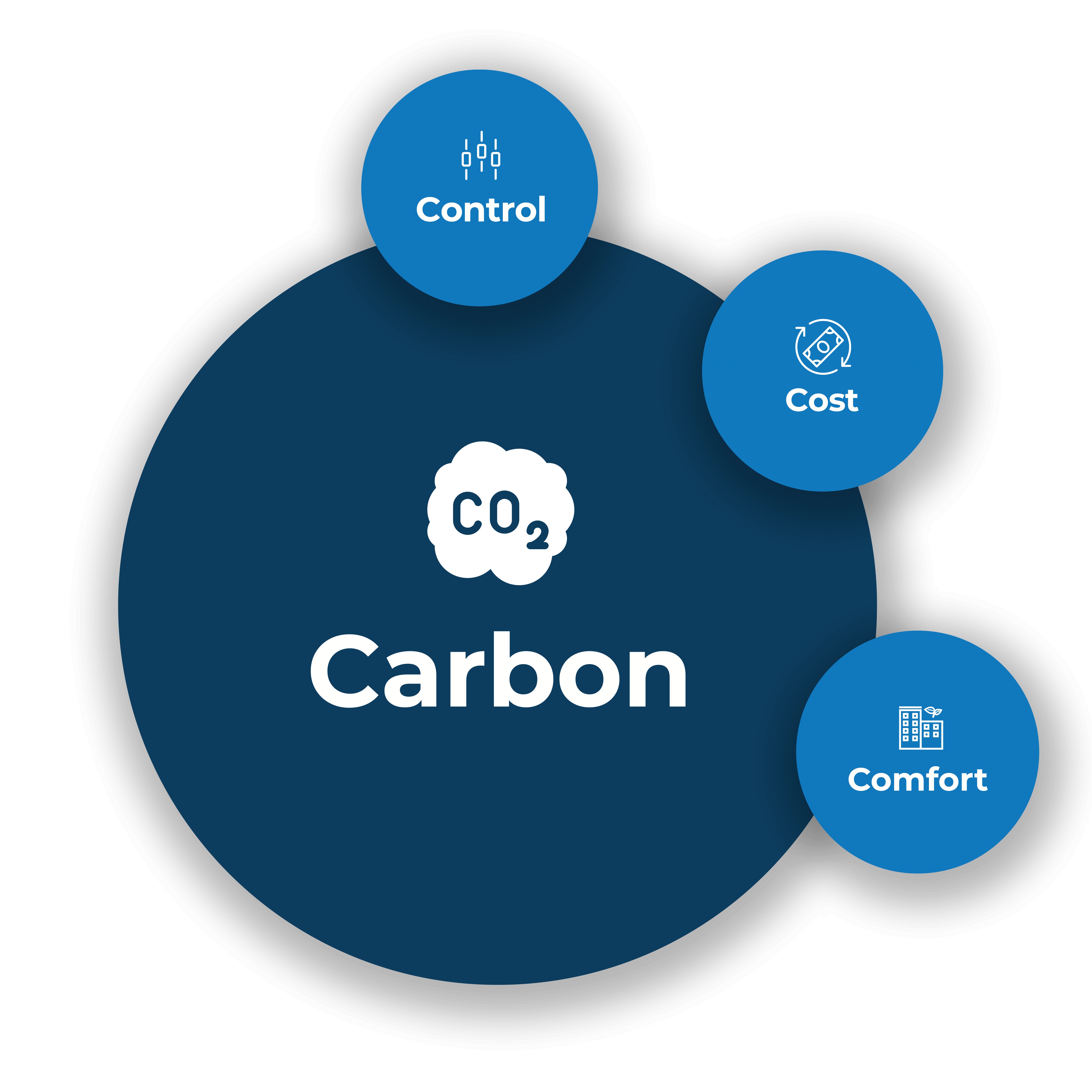